Laser Cutting machine manufacturer
- Electro-optic conversion efficiency is as high as 25%-30%.
- An excellent pulse power/energy stability.
- Long life, high precision, the service life of the pump sources are used to>100000 hours.
- Beam quality optimization in the application.
- Compact low-cost solutions to the semiconductor optical fiber laser in interface quality, no gas.
laser, green environmental protection. - Small volume, light weight, maintenance-free.
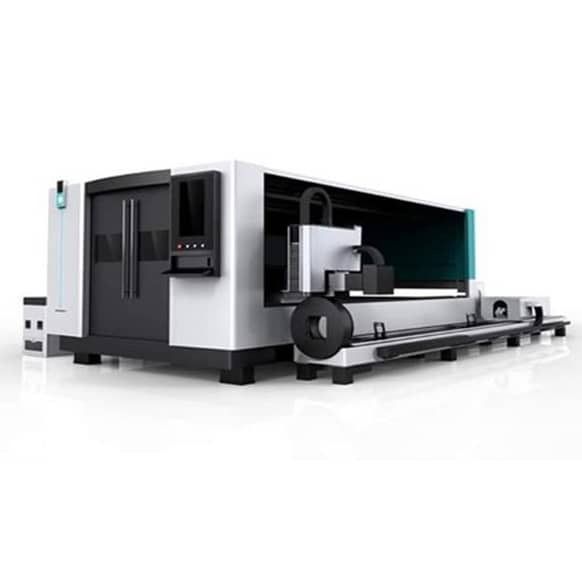
Laser Cutting Machine Hot Sale
The handheld laser welding machine can meet all of your cutting needs.
CNC laser cutting machine set machinery, electronic control, optics, software, and other professional technology in one, more integration of the air, water, lubrication system, the whole machine thousands of parts assembled. Any industrial system including the possibility of failure, fiber laser cutting machine can also occur.
Laser cutting is the best cutting method among all kinds of cutting techniques that people have mastered nowadays, the advantages of laser cutting are: small thermal deformation, high cutting accuracy, low noise, no pollution, ease to achieve automatic cutting, although the initial investment is large (disadvantages), but the processing cost less than 50% machining. Laser cutting as advanced manufacturing technology, the utility model has the advantages of a wide application range, flexible process, high processing precision, good quality, clean production process, easy realization of automation, flexibility, intelligentization, and improvement of product quality and labor productivity.
Unique advantages of fiber laser cutting
- The conversion efficiency is as high as 25%-30%!
- Excellent Pulse Power/energy stability
- Long life, high precision, pump source service life > 100,000 hours
- Faster, the effect more perfect.
- Beam quality optimization for applications
- Compact low-cost solutions to the semiconductor optical fiber laser in interface quality, no gas
laser, green environmental protection - Low-cost compact solution using semiconductor optical fiber as laser generation medium
Quality, without laser gas, green environmental protection. - Small size, lightweight, maintenance-free.
Application area and cutting ability.
1:Suitable for cutting space: two-dimensional plane cutting.
2:Application Industry: food machinery, kitchenware sanitary ware, elevator manufacturing, household appliances, food machinery, textile machinery, tool processing, automobile, decorative advertising, aerospace, shipbuilding, engineering machinery, locomotives, agricultural and forestry machinery, electrical manufacturing, petroleum machinery, laser external processing services and other machinery manufacturing and processing industries.
3:Cutting materials: carbon steel, stainless steel, aluminum alloy, brass, copper, acid wash plate, galvanized plate, silicon steel plate, electrolytic plate, titanium alloy, manganese alloy.
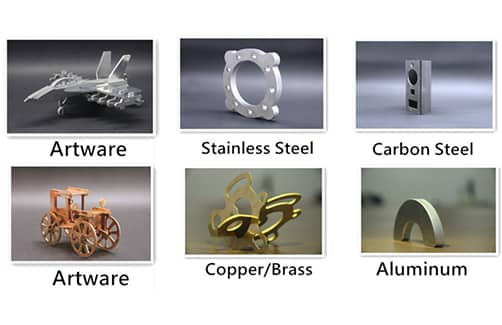
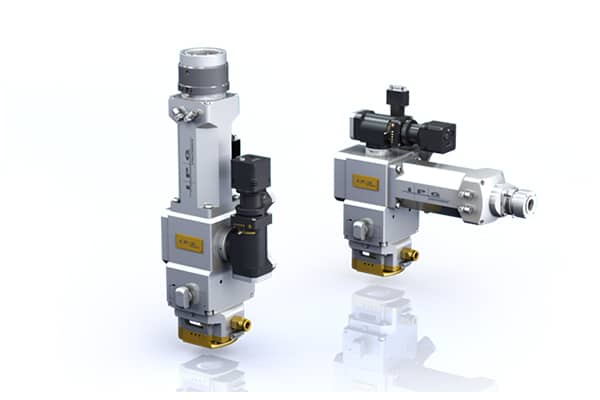
Introduction of fiber laser cutting head
The cutting head part adopts a laser fiber laser cutting head and capacitance non-contact automatic height tracking system. According to the physical characteristics of the fiber laser, the 5-inch focal length lens of the cutting head can be used for different thicknesses of the plate cutting, avoiding the trouble of changing different focusing mirrors. Also according to customer plate requirements to replace the appropriate lens.
Cutting Samples Under Different Laser Working Modes
Laser cutting is the best cutting method among all kinds of cutting techniques that people have mastered nowadays, the advantages of laser cutting are: small thermal deformation, high cutting accuracy, low noise, no pollution, easy to achieve automatic cutting, although the initial investment is large (disadvantages), but the processing cost less than 50% machining. Laser cutting as advanced manufacturing technology, the utility model has the advantages of wide application range, flexible process, high processing precision, good quality, clean production process, easy realization of automation, flexibility, intelligentization, and improvement of product quality and labor productivity
Fiber laser is a hot spot in the field of laser in recent years. In the field of processing fiber laser has the trend to replace the traditional YAG, C02 laser. It is generally believed that medium-power fiber lasers will be the third generation of the most advanced industrial processing lasers. Fiber laser has many unique advantages: good beam quality; small size, lightweight, maintenance-free; air cooling is easy to operate; low operation cost, can be used in an industrial environment; long life, high processing accuracy, high speed; high power conversion efficiency, it can realize intelligent, automatic, flexible operation and so on. According to the development of laser technology, fiber laser represents the development direction and trend of laser and has important application prospects in the industry, national defense, and other fields.
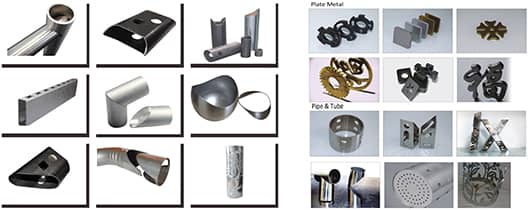
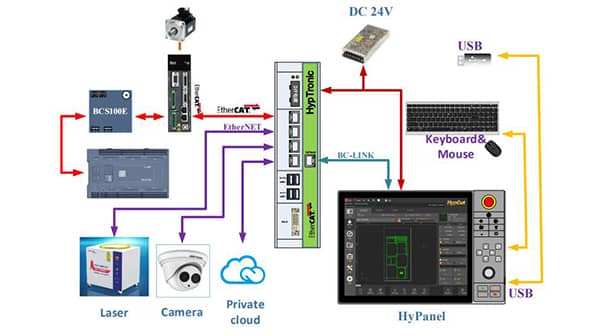
Structure of fiber laser cutting machine
The main machine is composed of a bed, cross beam, z Axis device, operation and control part, airway and waterway, etc.
1:Lathe bed part: Lathe bed adopts integral welding structure, after annealing to eliminate the internal stress, roughing it, finishing it after the second vibration aging treatment, it solves the stress caused by welding and machining well, the X, y, and z axes all adopt servo motor imported from Japan, equipped with high rigidity precision reducer, high precision gear rack, high precision linear guide rail and another high-efficiency transmission mechanism, the machine tool is equipped with the automatic lubricating device, the cutting area is equipped with dust-removing and smoke-removing device, and the bottom of the cutting area is equipped with a waste truck, which can pull out and clean the waste regularly.
2:Crossbeam: the Crossbeam is made of a lightweight casting structure, which is roughed after annealing to eliminate internal stress, and finished after secondary vibration aging treatment, which can solve the stress caused by casting and machining well, thus, the stability of the machine tool is greatly improved.
3. Z-axis up and down device is to achieve cutting head up and down movement. The capacitance sensor in the Z-axis device detects the distance between the cutting nozzle and the plate surface, then feeds the signal to the control system, which controls the up and down motion of the cutting head driven by the z-axis motor, thereby, the distance between the cutting nozzle and the plate is invariable and the cutting quality is effectively guaranteed.
6 Numerical control system.
1. Modular structure.
2. Integration, intelligence.
3. High speed, high precision.
4. Man-machine interface.
5. Full diagnostic function to quickly find the fault.
6. Status display and current position display.
7. Backoff function。
8. Breakpoint return function。
9. Leapfrog function。
10. Common edge cutting and other functions。
11. Multiple parts import mode.
12. Fast conversion and batch processing.
13. Efficient automatic typesetting function.
14. The process database can be set up according to different materials and thicknesses.
15. Support automatic cutting processing of multiple edges and corners.
16. Support for contour checking and complex graphics repair.
17. Automatic optimization of cutting path.
18. Perfect automatic process and flexible manual process.
19. Professional process display interface.
20. High software stability.
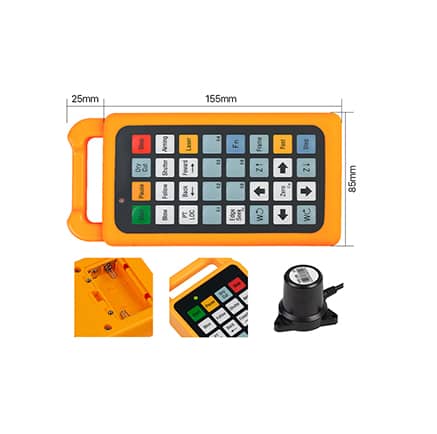
Application area and cutting ability
Take 8000 watts for example, cutting parameters (for reference only).
Cutting parameters (for reference only)
Cutting range and speed of each power | |||||||||
Power | Thickness (mm) | Maximum cutting speed m/min | |||||||
0.5-6 | Actual power | 0.5-2 | Actual power | Actual power | Actual power | ||||
CS(O2) | SS(N2) | Alu alloy(N2) | Brass(N2) | ||||||
500W | 1 | 8.0-11.0 | 6.0-8.0 | 2 | |||||
2 | 4.0-5.5 | 2.0-2.4 | 0.4-0.6 | ||||||
3 | 2.0-2.5 | 0.8-1.0 | |||||||
4 | 1.0-1.5 | ||||||||
5 | 0.7-1.0 | ||||||||
6 | 0.7-0.9 | ||||||||
8 | 0.3-0.5 | ||||||||
Power | Thickness mm | Maximum cutting speed m/min | |||||||
0.5-6 | Actual power | 0.5-2 | Actual power | Actual power | Actual power | ||||
CS(N2) | SS(N2) | Alu alloy(N2) | Brass(N2) | ||||||
700W | 1 | 16.0-18.0 | 12.0-16.0 | 10.0-12.0 | |||||
2 | 5.0-6.0 | 2.5-4.0 | 2.5-3.0 | ||||||
3 | 3.0-4.0 | 1.0-1.2 | 0.8-1.0 | ||||||
5 | 1.2-1.4 | ||||||||
6 | 1.0-1.2 | ||||||||
8 | 0.8-0.9 | ||||||||
Power | Thickness mm | Maximum cutting speed m/min | |||||||
0.5-10 | Actual power | 0.5-4 | Actual power | Actual power | Actual power | ||||
CS(O2) | SS(N2) | Alu alloy(N2) | Brass(N2) | ||||||
1000W | 1 | 20-30 | 18.0-24.0 | 12.0-16.0 | 12 | ||||
2 | 6.0-8.0 | 4.5-6.5 | 3.0-4.0 | 4 | |||||
3 | 4.0-5.5 | 2.0-2.5 | 2.5-3.5 | 1.5 | |||||
4 | 1.8-2.5 | 0.8-1.0 | 1.3-1.5 | ||||||
5 | 1.6-1.9 | 0.5-0.6 | |||||||
6 | 1.2-1.7 | ||||||||
8 | 1.0-1.1 | ||||||||
10 | 0.8-0.9 | ||||||||
12 | 0.6-0.75 | ||||||||
Power | Thickness mm | Maximum cutting speed m/min | |||||||
0.5-14 | Actual power | 0.5-5 | Actual power | Actual power | Actual power | ||||
CS(O2) | (N2) | Alu alloy(N2) | Brass(N2) | ||||||
1500W | 1 | 18.0-20.0 | 1500 | 20.0-25.0 | 1500 | 16.0-17.0 | 1500 | 8.0-12.0 | 1500 |
2 | 7.0-9 | 1500 | 6.5-7.0 | 1500 | 4.0-6.0 | 1500 | 4.0-5.0 | 1500 | |
3 | 4.0-5.0 | 1000 | 4.0-4.5 | 1500 | 2.5-3.0 | 1500 | 1.5-1.8 | 1500 | |
4 | 2.5-3.0 | 1300 | 2.0-2.5 | 1500 | |||||
5 | 1.6-2.0 | 1200 | 1.3-1.5 | 1500 | |||||
6 | 1.2-1.6 | 1200 | 0.7 | 1500 | |||||
8 | 1.0-1.2 | 1500 | |||||||
10 | 0.9-1.0 | 1500 | |||||||
12 | 0.7-0.8 | 1500 | |||||||
16 | 0.5 | 1500 | |||||||
Power | Thickness mm | Maximum cutting speed m/min | |||||||
0.5-16 | Actual power | 0.5-6 | Actual power | Actual power | Actual power | ||||
CS(O2) | SS(N2) | Alu alloy(N2) | Brass(N2) | ||||||
2000W | 1 | 25.0-35.0(N2) | 2000 | 28.0-32.0 | 1500 | 15.0-20.0 | 1900 | 14.0-15.0 | 1800 |
2 | 9.0-10.0(N2) | 2000 | 8.0-11.0 | 1800 | 8.0-9.0 | 1900 | 6.5-7.5 | 1800 | |
3 | 4.0-5.5 | 1000 | 4.0-5.0 | 1800 | 3.0-4.5 | 1900 | 3.0-3.5 | 1800 | |
4 | 3.0-4.0 | 2000 | 2.0-3.0 | 2000 | 2.0-2.5 | 1900 | 1.5-2.0 | 1800 | |
5 | 2.5-2.8 | 2000 | 1.5-2.0 | 2000 | |||||
6 | 1.6-2.0 | 2000 | 0.7-1.0 | 2000 | |||||
8 | 1.2-1.5 | 2000 | 0.5-0.6 | 2000 | |||||
10 | 1.0-1.2 | 2000 | |||||||
12 | 0.8-1.0 | 2000 | |||||||
16 | 0.7-0.8 | 2000 | |||||||
Power | Thickness mm | Maximum cutting speed m/min | |||||||
0.5-20 | Actual power | 0.5-8 | Actual power | Actual power | Actual power | ||||
CS(O2) | SS(N2) | Alu alloy(N2) | Brass(N2) | ||||||
3000W | 1 | 35(氮气) | 3000 | 30-42 | 3000 | 24-35 | 3000 | 18-21 | 2900 |
2 | 15(氮气) | 3000 | 18-23 | 3000 | 9-15 | 3000 | 8-12 | 2900 | |
3 | 4.0-5.0 | 2000 | 8-10 | 2800 | 5-7 | 3000 | 4-6 | 2900 | |
4 | 3.5-4.0 | 3000 | 4-6 | 3000 | 3-4.5 | 3000 | 2.5-4.0 | 2900 | |
5 | 3.0-3.5 | 3000 | 3-4 | 3000 | 2-2.6 | 3000 | 1.7-2.4 | 3000 | |
6 | 2.5-3.5 | 3000 | 2-3 | 3000 | 1.5-2.0 | 3000 | 1.0-1.6 | 3000 | |
8 | 1.6-2.0 | 3000 | 1.2-1.8 | 3000 | 0.7-0.9 | 3000 | 0.5-0.6 | 3000 | |
10 | 1-0-1.5 | 3000 | 0.8 | ||||||
12 | 0.9-1.0 | 3000 | |||||||
14 | 0.7-0.8 | 2000 | |||||||
16 | 0.6-0.7 | 2000 | |||||||
20 | 0.6 | 2000 | |||||||
Power | Thickness mm | Maximum cutting speed m/min | |||||||
0.5-20 | Actual power | 0.5-10 | Actual power | Actual power | Actual power | ||||
CS(O2) | SS(N2) | Alu alloy(N2) | Brass(N2) | ||||||
4000W | 1 | 35.0-38.0(N2) | 3000 | 60.0-65.0 | 4000 | 45.0-50.0 | 4000 | 55.0-60.0 | 4000 |
2 | 15.0-18.0(N2) | 3000 | 26.0-28.0 | 4000 | 20.0-23.0 | 4000 | 23.0-25.0 | 4000 | |
3 | 4.5-5.0 | 2000 | 10.0-11.0 | 4000 | 11.0-12.0 | 4000 | 9.0-10.0 | 4000 | |
4 | 3.5-4.0 | 3000 | 7.5-8.2 | 4000 | 5.0-8.0 | 4000 | 5.5-6.5 | 4000 | |
5 | 2.7-3.5 | 3000 | 4.5-5.5 | 4000 | 3.5-4.0 | 4000 | 3.0-3.5 | 4000 | |
6 | 2.6-3.0 | 4000 | 3.0-4.0 | 4000 | 2.5-3.5 | 4000 | 2.0-2.2 | 4000 | |
8 | 1.6-2.0 | 4000 | 1.3-1.5 | 4000 | 1.0-1.2 | 4000 | 0.8-1.0 | 4000 | |
10 | 1.0-1.5 | 4000 | 1.0-1.1 | 4000 | 0.5-0.6 | 4000 | |||
12 | 0.9-1.0 | 4000 | 0.6-0.75 | 4000 | |||||
14 | 0.7-0.8 | 2000 | |||||||
16 | 0.6-0.7 | 2000 | |||||||
20 | 0.6-0.7 | 2000 | |||||||
Power | Thickness mm | Maximum cutting speed m/min | |||||||
0.5-25 | Actual power | 0.5-16 | Actual power | Actual power | Actual power | ||||
CS(O2) | SS(N2) | Alu alloy(N2) | Brass(N2) | ||||||
6000W | 1 | 35.0-38.0(N2) | 3000 | 60.0-65.0 | 4000 | 45.0-50.0 | 4000 | 55.0-60.0 | 4000 |
2 | 15.0-18.0(N2) | 3000 | 35.0-42.0 | 6000 | 30.0-36.0 | 6000 | 28-30 | 6000 | |
3 | 4.5-5.0 | 2000 | 15.0-17.5 | 6000 | 16.0-18.0 | 6000 | 13.5-15.0 | 6000 | |
4 | 3.5-4.0 | 3000 | 11.0-12.5 | 6000 | 7.5-12 | 6000 | 7.0-9 | 6000 | |
5 | 2.7-3.5 | 3000 | 6.5-8.0 | 6000 | 5.0-6.0 | 6000 | 4.5-5.2 | 6000 | |
6 | 2.6-3.0 | 4000 | 4.5-6.0 | 6000 | 3.5-4.5 | 6000 | 3.0-3.3 | 6000 | |
8 | 2.0-2.6 | 4000 | 1.9-2.2 | 6000 | 1.5-1.8 | 6000 | 1.2-1.5 | 6000 | |
10 | 1.4-2.0 | 4000 | 1.5-1.6 | 6000 | 1.2-1.4 | 6000 | 1.0-1.1 | 6000 | |
12 | 1.3-1.6 | 4000 | 0.9-1.1 | 6000 | 0.8-1.0 | 6000 | 0.7-0.9 | 6000 | |
14 | 1.2-1.5 | 2500 | 0.7-0.8 | 6000 | 0.5-0.7 | 6000 | |||
16 | 1.0-1.2 | 2500 | 0.5-0.7 | 6000 | |||||
20 | 0.7-0.9 | 2500 | |||||||
26 | 0.5-0.6 | 4000 | |||||||
Remarks | CS=Carbon Steel,SS=Stainless Steel,Alu alloy=Aluminium alloy,N2=Nitrogen gas | ||||||||
Technical Parameters
Technical parameter of machine tool (Take 8,000 6020 watts example)
Processing area and scope | |
Working surface (length * width) | 6000mm*2000mm |
X-axis travel | 2020mm |
Y-axis travel | 6020mm |
Z-axis travel | 200mm |
Precision | |
X/Y positioning accuracy | ±0.10mm/m |
X/Y repeat positioning accuracy | ±0.10mm/m |
Z-axis positioning accuracy | ±0.05mm/m |
Precision of Z-axis repetitive positioning | ±0.05mm/m |
Speed | |
X/y maximum positioning speed | 120m/min |
Power parameter | |
Phase number | 3 |
Rated voltage of power supply | 380V |
Frequency | 50HZ |
Protection level of total power supply | IP54 |
Weight and size | |
Maximum load of worktable | 3000KG |
Dimensions (length * width * height) | 16500mm*3800mm*2300mm |
Primary Configuration
No. | Brand name | Brand/parameters | Notes |
1 | Laser source | IPG-YLS8000W | |
2 | System | HYPCUT / BECKHOFF | Optional match |
3 | Cutting head | Precitec (Original German autofocus) | |
4 | Focusing lens set | Precitec(Original German autofocus) | |
5 | Collimator set | Precitec(Original German autofocus) | |
6 | Servo motor | YASKAWA / BECKHOFF | Optional match |
7 | Servo Drive | YASKAWA / BECKHOFF | Optional match |
8 | Gear wheel | ALPHA | |
9 | Rack | YYC/CST/APEX | |
10 | Speed reducer | ALPHA | |
11 | Linear Guide | HIWIN/TBI | |
12 | Proportional valve | SMC | |
13 | Solenoid valve | SMC | |
14 | Machine tool solenoid valve | SMC | |
15 | Pneumatic control valve | SMC | |
16 | Air pressure alarm switch | SMC | |
17 | Tricolor lamp | APT | |
18 | Air cylinder | SMC | |
19 | Open circuit protection switch | Schneider | |
20 | Contactor | Schneider | |
21 | Relay | Schneider/ Phoenix | |
22 | Filter | Shanghai Huitong | |
23 | Terminal connector | Phoenix | |
24 | Limit switch | OMRON、YANGMING | |
25 | Motor Cable | igus | |
26 | Limit Cable | igus | |
27 | Encoder cable | igus | |
28 | PLC | MITSUBISHI | |
29 | Frequency converter | DELTA | |
30 | Switching power supply | Heng fu | |
31 | Drag chain | igus | |
32 | Cabinet air conditioning | Well-known domestic brands | |
33 | Water Chiller | Well-known domestic brands | |
34 | Dust blower | Made in China | |
35 | Bed | JTClaser |
Frequently Customer Enquiry
Most frequent questions and answers about the fiber laser cutting machine
What is a fiber laser cutter and what can be done?
Laser cutting is the best cutting method among all kinds of cutting techniques that people have mastered nowadays, the advantages of laser cutting are: small thermal deformation, high cutting accuracy, low noise, no pollution, easy to achieve automatic cutting, although the initial investment is large (disadvantages), but the processing cost less than 50% machining. Laser cutting as advanced manufacturing technology, the utility model has the advantages of wide application range, flexible process, high processing precision, good quality, clean production process, easy realization of automation, flexibility, intelligentization, and improvement of product quality and labor productivity!
Fiber laser cutting machine can cut how much size of the product?
Strictly speaking: Suitable for cutting space: two-dimensional plane cutting;
Application Industry: food machinery, kitchenware sanitary ware, elevator manufacturing, household appliances, food machinery, textile machinery, tool processing, automobile, decorative advertising, aerospace, shipbuilding, engineering machinery, locomotives, agricultural and forestry machinery, electrical manufacturing, petroleum machinery, laser external processing services and other machinery manufacturing and processing industries.
What materials can fiber laser cutting machine cut?
Carbon steel, stainless steel, aluminum alloy, brass, copper, acid wash plate, galvanized steel, silicon steel plate, electrolytic plate, titanium alloy, manganese alloy.
Can large workpieces be cut by fiber laser cutting machine?
Yes, any shape of metal products can be accurately cut by a fiber laser cutting machine.
What is the cutting effect of the fiber laser cutting machine?
The advantages of laser cutting are small thermal deformation, high cutting accuracy, low noise, no pollution, easy to realize automatic cutting.
Does the cut need to be polished again after cutting?
Laser cutting as advanced manufacturing technology, with a wide range of applications, flexible technology, high precision processing, good quality, production process clean and easy to achieve automation, flexibility, intelligence and improve product quality, cutting effect smooth and bright, no need to reprocess processing labor productivity and other advantages.
What are the consumables for a fiber laser cutting machine?
Electricity, nitrogen, argon, air.
Is it safe to use a laser cutting machine?
CNC laser cutting machine set machinery, electronic control, optics, software, and other professional technology in one, integrated air, water, lubrication, and other systems, the appearance of a fully closed integrated cabinet, very safe.