Three methods of suppressing porosity in laser welding aluminum alloy
Aluminum alloy is widely used in the automobile industry, new energy, aerospace, and construction industry because of its low density, high strength, and good corrosion resistance. At present, laser welding has been widely used in the production and manufacture of aluminum alloy products. Compared with the traditional welding method, laser welding can provide higher production efficiency and better weld quality, high precision welding, and automation of complex structures are realized.
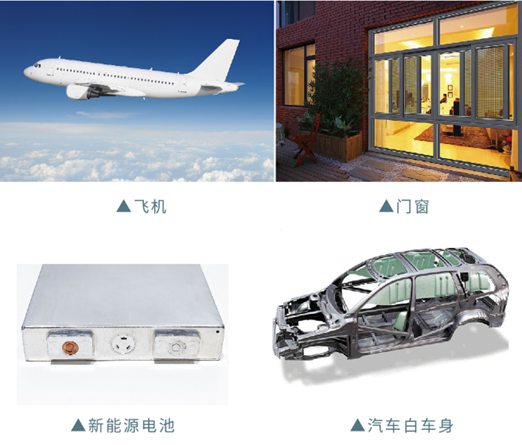
Laser welding is a kind of technology that radiates high-intensity laser to the metal surface and makes the metal melt and then cool and crystallize to form the weld through the thermal-mechanical coupling between laser and metal. According to the thermal mechanism of laser welding, there are two kinds of heat conduction welding and deep penetration welding, heat conduction welding is mainly used in the package welding of precision parts or micro-nano welding, and laser deep penetration welding is mainly used in the welding of materials that need full penetration, the welding process will vaporize the material and keyhole appears in the molten pool, which is the most widely used laser welding method and the first choice for aluminum alloy welding.
Laser fusion welding features:
Advantages: laser welding aluminum alloy using swing laser welding, no additional materials, welding equipment is simple, no consumables, easy to automation;
Disadvantages: high requirements for welding clearance, otherwise the weld is easy to collapse; the welding starting point and endpoint easy to focus; welding process stability, easy to produce welding defects;
Case: Welding of series 5 aluminum alloy door frame in building decoration industry
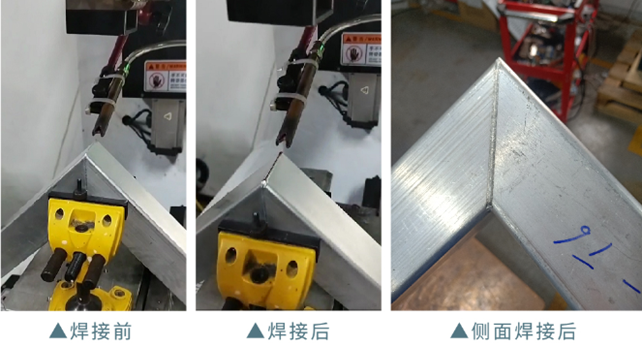
Due to the inherent physical properties of aluminum alloys, for example, for low absorption of laser, the low boiling point of alloy elements, high thermal conductivity, high Coefficient of thermal expansion, relatively wide solidification temperature range, high solidification shrinkage, low viscosity, and high hydrogen absorption in the liquid state, etc., so in the process of laser welding, it is easy to produce defects such as blowhole, hot crack and so on.
Porosity is one of the most common defects in the laser welding of aluminum alloy. It can destroy the compactness of the weld metal, weaken the effective cross-section area of the weld, and reduce the mechanical properties and corrosion resistance of the weld, therefore, effective measures must be taken to prevent porosity and improve the internal quality of the weld.
Suppression of porosity by laser fusion welding:
- Restrain the welding blowhole by the way of surface treatment before welding
The surface treatment before welding is an effective method to control the porosity in laser welding of aluminum alloy.
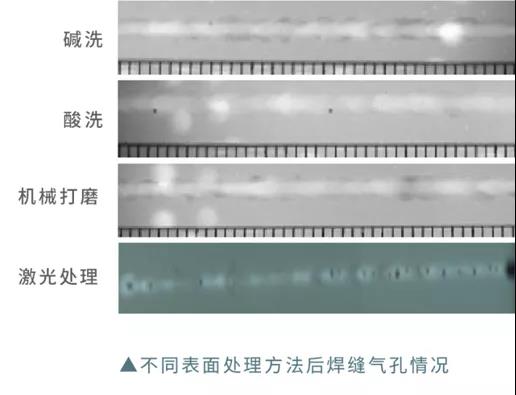
By contrast, the chemical treatment of the test plate surface (metal cleaning agent cleaning-water washing-alkali washing-water washing-acid washing-water washing-drying) process of the best. Among them, 25% NaOH (sodium hydroxide) aqueous solution was used to remove the surface thickness of the material, and 20% HNO3(nitric acid) + 2% HF (hydrogen fluoride) aqueous solution was used to neutralize the residual alkaline solution for acid cleaning. After surface treatment, the test plate is welded within 24 hours. After treatment, the test plate is assembled before welding and then wiped with anhydrous alcohol.
- The welding porosity is suppressed by welding process parameters
The formation of Weld Blowhole is related not only to the surface treatment quality of welding parts but also to the welding process parameters. The influence of welding parameters on weld porosity is mainly reflected in weld penetration, i. e. the influence of weld back width ratio on weld porosity.
The results show that the concentration distribution of chain porosity can be effectively improved when the back width ratio r > 0.6, and the existence of large porosity can be effectively improved when the back width ratio r > 0.8, the porosity in the weld is eliminated to a great extent.
- Restrain welding blowhole by selecting correctly protective gas and flow rate
During laser welding, the proper blowing of shielding gas can effectively reduce the weld porosity.
As shown above, Ar (argon) and He (helium) are used to protect the weld surface. In laser welding of aluminum alloy, the degree of ionization of AR and He to the laser is different, resulting in different weld formation. The results show that the porosity of the weld using AR as shielding gas is less than that using He as shielding gas.
At the same time, we should also pay attention to the small gas flow (< 10L/min) welding produces a large number of plasma that can not be blown away, which makes the welding pool unstable and increases the probability of porosity formation. The gas flow rate is moderate (about 15L/min), the plasma is effectively controlled, the protective gas has a good anti-oxidation effect on the solution pool, and the pores are the least. The gas flow rate is too high and the gas pressure is too high, so some of the protective gas is mixed into the solution pool and the porosity is increased.
It is a difficult problem to suppress the porosity of aluminum alloy by laser welding. Because of the influence of aluminum alloy material, the porosity of aluminum alloy can not be avoided completely in the welding process. Through the process optimization before and after welding, we summarize the experiment and put forward 3 kinds of ways to restrain the blowhole for the reference of colleagues in the industry. Chuangxin laser not only focuses on the research and innovation of laser product technology, but also explores various laser processing technology, and looks forward to discussing with more industry experts to promote the laser processing technology in China.